Accomplish Perfection: Navigating in Casting Aluminum Illinois
Accomplish Perfection: Navigating in Casting Aluminum Illinois
Blog Article
Accuracy and Excellence: Best Practices for Successful Light Weight Aluminum Spreading
In the world of aluminum casting, accomplishing precision and perfection is not merely a goal but a standard that differentiates quality. The careful process of aluminum casting demands attention to detail at every phase, from product option to last finishing touches.
Material Selection
When considering product option for aluminum casting procedures, longevity, and warm resistance are critical factors to evaluate,. Light weight aluminum alloys use a wide variety of alternatives, each with special residential properties that can considerably impact the top quality and performance of the final casted product. One usual option is the 356 alloy, known for its superb fluidity and resistance to deterioration, making it appropriate for a variety of applications. For high-stress settings requiring remarkable stamina, the 7075 alloy stands out as a result of its high strength-to-weight ratio. In addition, the 6061 alloy is favored for its excellent weldability and formability, making it a flexible alternative for elaborate layouts.
In the option process, it is crucial to think about not only the mechanical properties of the alloy yet also its thermal attributes. Heat resistance is important to make certain that the casted part can hold up against the temperatures it will be subjected to during operation without jeopardizing its structural stability. By very carefully reviewing the durability and warmth resistance of different aluminum alloys, manufacturers can make informed choices that cause high-quality, reliable casted items.
Mold Layout
In the world of light weight aluminum casting best techniques, an integral facet that dramatically affects the end product's quality and integrity is the meticulous design of the mold and mildew. Mold and mildew design plays an essential role in determining the dimensional precision, surface finish, and total ins and out of the cast aluminum component. When producing a mold for light weight aluminum casting, several vital aspects should be thought about to make sure optimal outcomes.
First of all, the mold layout ought to account for the product flow features of molten light weight aluminum to avoid defects such as contraction, porosity, or misruns. Proper gating and riser positioning are vital elements in the mold and mildew design procedure to facilitate smooth steel circulation and reduce the development of air pockets.
Furthermore, the mold and mildew style need to consider the cooling price of the aluminum to avoid cracking or distortion throughout solidification. Appropriate venting and cooling networks within the mold can assist manage the temperature distribution and advertise uniform solidification of the metal.
Process Optimization
To boost performance and top quality in light weight aluminum spreading, procedure optimization plays a pivotal function in making best use of and streamlining procedures result. By fine-tuning each action of the spreading procedure, makers can determine bottlenecks, decrease waste, and enhance overall productivity.
In addition, applying lean Full Report production concepts can further boost procedure optimization in light weight aluminum casting. By getting rid of non-value-added activities and focusing on continuous renovation, makers can accomplish higher performance degrees and better source use. Furthermore, regular surveillance and evaluation of key efficiency indicators (KPIs) aid in recognizing areas for renovation and making data-driven choices to optimize the spreading process continually.
Top Quality Control
Process optimization in light weight aluminum casting not just enhances performance and efficiency but likewise lays the foundation for rigid high quality control actions to maintain industry requirements. Quality control is vital in making sure that final light weight aluminum castings satisfy the required specs and efficiency criteria. Applying an extensive high quality control process includes various actions, beginning from the preliminary layout phase with to the last inspection of the cast components.
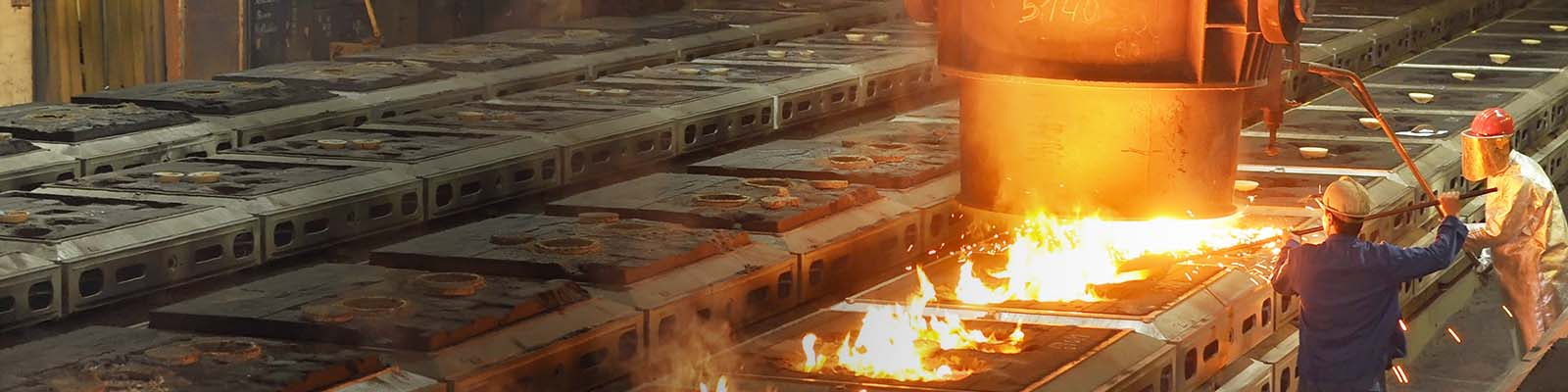
Additionally, developing official source clear high quality control protocols and documents procedures is essential for monitoring and checking the casting procedure. By preserving detailed documents of production specifications, testing outcomes, and assessment records, manufacturers can guarantee consistency and traceability in their light page weight aluminum casting procedures. Complying with rigorous quality assurance techniques not only boosts the overall dependability of aluminum castings yet also imparts self-confidence in customers pertaining to the quality of the end products.
Finishing Methods
Just how can aluminum spreading be boosted through thorough application of completing strategies? Finishing methods play a critical role in raising the top quality and visual appeals of aluminum spreadings. Among the primary methods utilized is surface area smoothing, which involves the removal of any kind of blemishes or rough edges to achieve a perfect surface. This procedure not just boosts the visual appeal of the spreading yet likewise improves its total functionality by making certain harmony and accuracy.
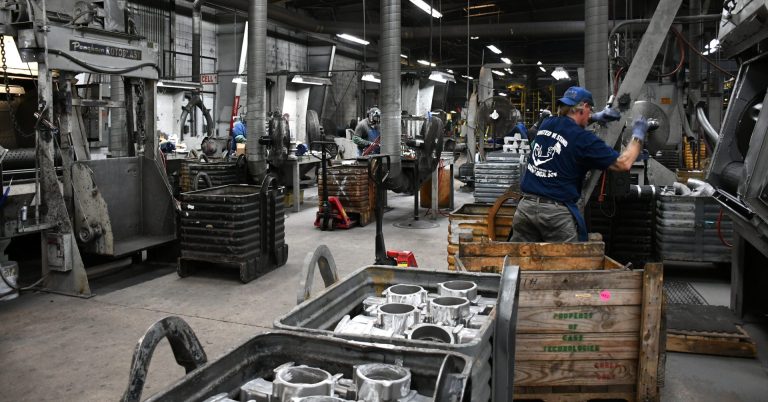
Additionally, strategies like powder covering or painting can be used to aluminum castings to give both aesthetic charm and added protection against ecological factors. By thoroughly picking and using the suitable finishing methods, suppliers can ensure that their aluminum castings fulfill the highest possible standards of high quality and efficiency.
Verdict
Finally, successful aluminum casting requires precision and perfection in material choice, mold and mildew layout, procedure optimization, quality control, and finishing techniques. By complying with finest methods in each of these locations, suppliers can ensure top notch and regular results in their aluminum casting processes. casting aluminum illinois. It is vital to pay interest to every detail and continuously pursue improvement to achieve optimal end results in light weight aluminum spreading
The thorough procedure of light weight aluminum casting demands attention to detail at every phase, from product choice to final finishing touches.To enhance efficiency and high quality in aluminum casting, procedure optimization plays a crucial duty in enhancing operations and taking full advantage of result.Refine optimization in aluminum casting not just boosts performance and efficiency but additionally lays the structure for strict quality control actions to maintain industry criteria.One vital aspect of top quality control in light weight aluminum spreading is the use of advanced screening methods to assess the stability and homes of the castings.In verdict, successful light weight aluminum casting calls for precision and excellence in material choice, mold and mildew style, procedure optimization, high quality control, and ending up strategies.
Report this page